Yellow Belt Module
Get the whole idea of what our modules are about
List of Yellow Belt Module
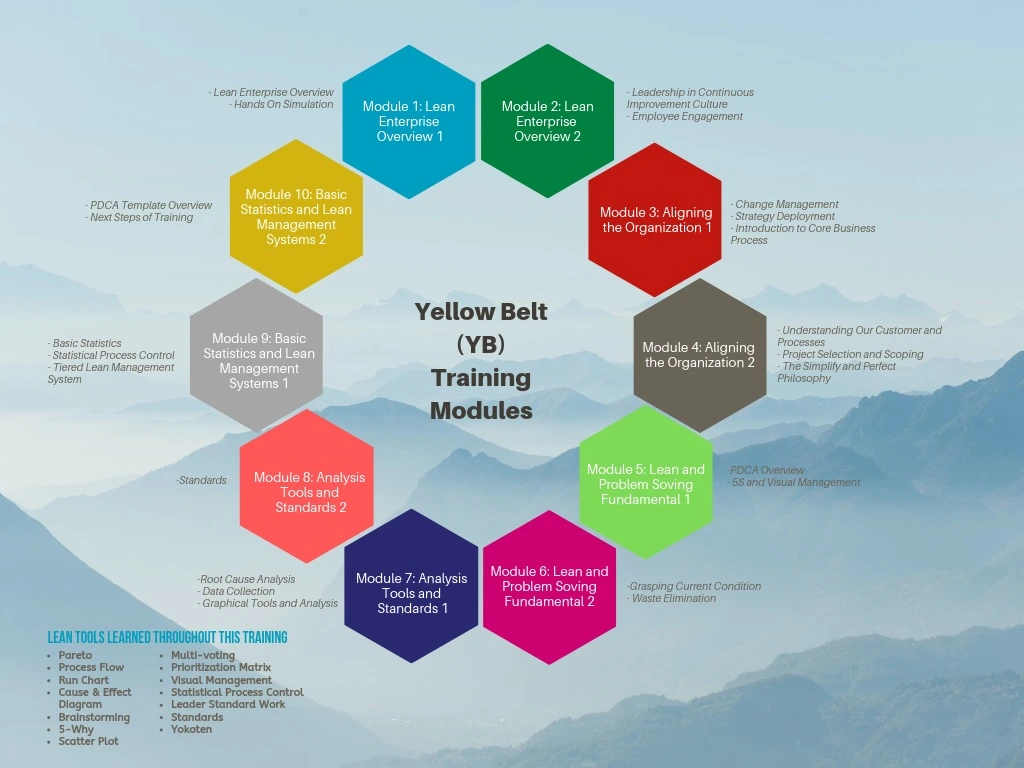
Overview of Yellow Belt
Module 1 - Lean Enterprise Overview
Student have been introduced to the basic knowledge of lean such as the overview of the Bose Lean Enterprise Vision and House of Bose. They are also delighted to experience training and sharing sessions from Mr. Teh Wei Huai, alumni of Lean Six Sigma Wave 2 who is currently working as an R&D Project Manager at Keysight Technologies Malaysia Sdn Bhd. Mr. Teh Wei Huai ran a fun simulation game with six runs using Lego to simulate the assembling process in a Legoliv manufacturing line. Students used lean tools such as 5S, Pull System, SMED, Level Loading, and Takt Time to enhance each run during the simulation. They are also learning how each lean tool improvement affects the financial performance of an assembly/production line.
Module 2 - Lean Enterprise Overview
This module is about Leadership in a Continuous Improvement Culture. Students have a sharing session with Mr Saharom who is a Business Excellence Manager from Flextronics Systems Penang Sdn. Bhd. in Batu Kawan with 22 years of working experience and almost 10 years of experience specifically on Lean Six Sigma. He shares how companies work by implementing lean and six sigma in their management system. Mr Mohammad Shafiq Bin Omar who is an alumnus of Lean Six Sigma Wave 8 shares about management and leadership and discusses 'Kata' which is a routine that we practice deliberately until it becomes a habit. Associate Professor Ir. Dr Chin Jeng Feng who is one of the main instructors for this program has elaborates on the characteristics of lean leaders which was an eye-opener for all of the students.
Module 3 - Aligning the Organization
This session was conducted via the Webex meeting platform by Mr. Wong Bak Hock who is also an alumnus of Lean manufacturing wave 1 and also Dr. Hasnida. Mr. Wong currently working at Jabil as an Industrial Engineer. He explains in-depth about Lean Manufacturing through topics such as changes in management, strategy deployment, and core business process throughout the session. Mr. Wong uses interactive material such as videos and figures to make a better understanding of the topics. He also shared a lot of tips and experiences in the Q&A sessions.
Module 4 - Aligning the Organization
This module is about understanding customers and processes. "Our Customers Are the Beginning of Lean Enterprise." It is all about the consumer in business. Without clients, no business can survive. Dr. Amalina discussed this topic, and students learnt the importance of hearing the customer's voice and its worth from the customer's perspective. Students also learnt how to create an IPO, SIPOC, and Value Stream Map (VSM), which depicts the process flow in the most simplistic way possible. Luqman Haikal Mohamad Nizar, a former Lean Six Sigma Wave 8 student, was also active in teaching topics such as Project Selection and Scoping, as well as Simplify and Perfect. Students were exposed to the concepts of SMART Goals, Project Prioritization Matrix, and process improvement.
Module 5 - Lean and Problem-solving
Fundamental
Do you know how to apply the PDCA approach to solve problems and enhance organisational processes? The Yellow Belt Lean Six Sigma training covers the topic of Lean and Problem-Solving Fundamentals 1. Ts. Dr. Muhammad Hafiz Bin Hassan led the first session, in which students learnt about the Plan, Do, Act, and Check (PDCA) technique and its 12 phases. Puan Hasnah Binti Hassan, a Penolong Pegawai Tadbir from BHEPA Kampus Kejuruteraan, then led the second session. She provided a thorough overview of the 5S and Visual Management approaches used to create a visually appealing workplace. Under the supervision of Dr Nur Amalina and a few seniors from Wave 8, the students also studied and practised organised problem solving using Help Simulation. The goal of this simulation game is to have a thorough grasp of how PDCA thinking and lean foundation elements contribute to continuous improvement operations.
Module 6 - Lean and Problem-solving
Fundamental
The Plan-Do-Check-Act (PDCA) cycle is a change management approach. It is a critical component of the lean manufacturing concept and a necessary precondition for continual improvement of people and processes. The workshop begins with graduates from Wave 8 (Mohamad Ridzuan) and Dr Amalina teaching about the first three phases of the PDCA application's Plan phase. This session covers "Define and Breakdown Problem," "Grasping the Current Condition," "Set a Target Condition," and "Waste Elimination". Students are also learning about process maps, graphic analysis (run charts), and SMART goals. In HELP practical simulation Round 3, students used their expertise to identify a few performance improvements. They have extensive expertise and knowledge on how to carry out changes utilizing the PDCA and waste elimination methodologies.
Module 7 - Analysis Tools and Standards
The session began with Dr. Amalina and Wave 1-alumni Mr. James teaching about the third and fourth steps in the plan phase of the PDCA application. (The Plan-Do-Check-Act (PDCA) cycle is a method of change management. It is an essential component of the lean manufacturing concept and a prerequisite for ongoing development of people and processes.) We were shown how to use tools like "5 Why" and "Cause & Effect Diagram" to identify core reasons. Students were also taught to one of the graphical analysis approaches, the Pareto chart. Students were given a package of "m&m's" milk chocolate and instructed to create a pareto chart. Mr. James then led a session in which students learned about "Selecting the Process." In this case, data collecting is crucial, and students gained a better knowledge of the importance of data collection, data types, and fundamental calculations.
Module 8 - Analysis Tools and Standards
One of the most fundamental aspects to a successful PDCA—a problem-solving strategy for continuous improvement—is discipline. In the session with Associate Professor Ir. Dr. Chin Jeng Feng, students received a lot of advice on both theory and practical experience. They were taught about the stages "Identify, Develop & Test, Refine & Finalize, and Implement Countermeasures." They recognise that following "Implement," keeping track and following up is critical since it reflects the effort of the implementation and aids in deciding what to do next. Then they concentrated on process standardisation and stabilisation as a key to preventing regression during progress. Students must establish, maintain, and enhance the standard, since there is always opportunity for improvement. Under the supervision of Dr Amalina and Dr Hasnida, students applied all of these ideas to the Final Run of the HELP simulation. This improves our understanding by putting ideas into practise. The main point of the day is "Standardization is the first step toward progress. There can be no progress if there is no standard "by Taiichi Ohno, Toyota Production System's father.
Module 9 - Basic Statistic and Lean Management Systems
This class consists of two sessions. Dr. Hasnida Binti Ab Samat gave the first session on basic statistics. Students learned how to create a histogram and control charts during this lesson. They discovered that control charts and SPC successfully convert data into valuable information. Control charts/SPC are a tool for maintaining gains and indicating when anything has changed in the process. It also alerts users when a process is deteriorating. Dr. Nur Amalina Binti Muhammad introduced the PDCA 12-step template in the second session. This session is a refresher of all 12 stages in PDCA, with numerous questions being asked from steps 1 to 12 to ensure that we understand each step in PDCA. Students also participated in "Let's Play: Jeopardy!" It's a fun game to play and a wonderful test to assess how well students recall what they've studied in EPE432 Lean Six Sigma Manufacturing.